Ever wonder what separates manufacturing giants from companies stuck in endless firefighting mode? It’s rarely just luck or tech. Most of the time, it’s an invisible checklist at work: a way of thinking that brings order to the chaos. That’s where the 5 Ps of manufacturing come in. Not exactly top-secret, but not always obvious, this formula shapes everything from your grandma’s kitchen to Tesla’s gigafactories. Miss just one P, and suddenly you’re swimming in delays, quality headaches, or costs that spiral out of control. Nail them all, and you’ve got a shot at the kind of efficiency and reputation that keeps customers coming back.
People: The Human Engine Behind Every Process
Factories hum because of the people on the floor, not the machines. The best manufacturing setups know this, and they invest in their teams. Sure, automation is growing—over 2.7 million industrial robots were in use by the end of 2024 worldwide, according to the International Federation of Robotics—but even the flashiest robot still needs a savvy human behind the controls. Skilled workers can spot a problem before it becomes a disaster. They tweak routines for better output. They save you from costly mistakes. It's not about hiring the most people, but having the right ones in the right roles—with training that keeps them sharp as technology evolves.
Working conditions matter a ton. Poor lighting, noise, or temperature extremes drain energy and attention, leading to mishaps. Did you know bad ergonomics can tank productivity by almost 25% in some industries? Giving people a say in how things run, listening to frontline feedback, and rewarding initiative change everything. When people care, defects drop, and improvements skyrocket. Every manufacturer has a story of a worker’s tiny suggestion saving millions down the line. If you're looking for inspiration, Toyota’s famous "Kaizen" system generated over 60,000 suggestions per year from employees, many of which became company-wide improvements.
Also, don't overlook leadership. Epic manufacturing meltdowns often trace back to unclear direction, a lack of training, or poor communication. Define clear expectations. Spend time with your team. Or better yet, try a Gemba walk—Japanese for “the real place”—where managers step out onto the plant floor to see processes with their own eyes. This simple move has turned many floundering operations around, thanks to personal connection and real-time problem-solving.
Process: The Blueprint for Consistent Quality
Think of process as your manufacturing playbook. Without it, you’re guessing. With it, you create predictable outcomes. It covers everything—how raw materials are received, how products move through different workstations, and the steps for final inspection. It’s tempting to go with “the way we’ve always done it,” but those habits often hide efficiency black holes. Mapping out your process makes it easier to find bottlenecks. The American Productivity & Quality Center says companies that chart their processes find and fix problems 40% faster.
Good process is all about the details—a tweak in machine setup or how parts are stocked can slash lead time. The gold standard here is standard operating procedures (SOPs). Written right, these are simple, visual, and easy to follow even on a busy shop floor. A team member should spot mistakes instantly because the steps and checks are laid out. This also helps when onboarding new employees; nobody wants to sit through a 100-page manual. Visual work instructions with photos cut training times by up to 60%, according to an industrial training study from 2023. Make your process visible to everyone. Production boards, dashboards, even real-time data projected on the wall—these keep progress clear and problems out in the open before they snowball.
Maybe you’ve heard “process improvement” thrown around. It’s not a cliché—it’s a mindset. Lean manufacturing, Six Sigma, and continuous improvement playbooks have raised global efficiency standards for decades. Lean’s “value stream mapping” is one of the fastest ways to spot wasted steps and excess movement. Even if you’re a tiny shop, taking one afternoon per month to walk through your process with the team uncovers quick wins. Don’t forget documented customer feedback—what’s broken after shipping, what keeps getting returned—to close the loop and make your process bulletproof.
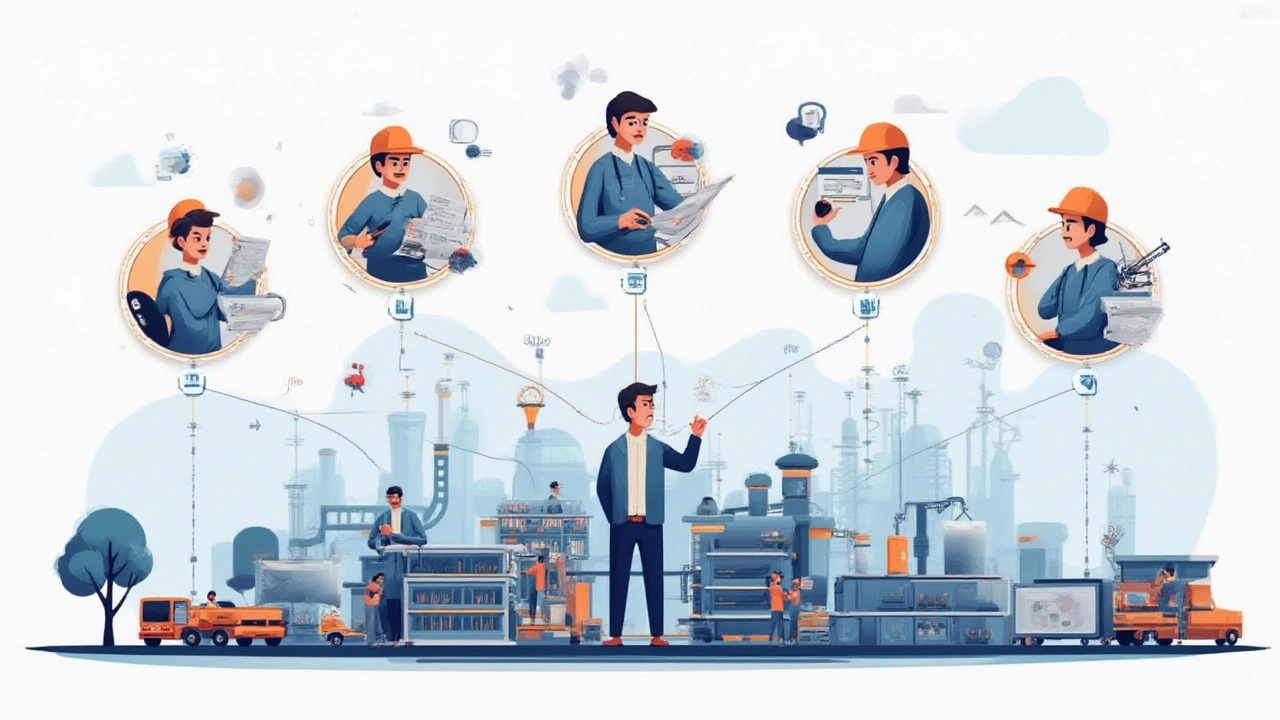
Product: Matching Design to Real-World Demands
Every manufacturer faces a brutal reality: even a flawless process won’t save you if your product doesn’t deliver what customers want. The product P is about crystal-clear specifications, quality standards, and understanding what the end user truly cares about. In 2022, 34% of global recalls in food manufacturing were due to wrong labeling—not contamination or spoilage. That’s a product issue, not a process problem.
You want a product that’s sturdy, simple to assemble, and meets all regulations. This starts at the design phase. Cross-functional teams—engineers in one corner, sales in another, shop floor staff at the table—spot design issues that the drawing board might miss. For example, asking a welder how to simplify a joint can shave hours off assembly every week. GE Appliances famously saves over $15 million per year just by inviting front-line workers to give design feedback before a product launch.
Consistency is the secret weapon here. Suppliers must meet exact specs every time—“pretty close” won’t fly if a part fails under stress. Track every product’s journey with a traceability system. This means barcodes, digital logs, or QR codes, ensuring if something goes wrong in the field, you know exactly which batch to look at. Automotive manufacturers lead the way in traceability: regulations often require tracking parts from origin through assembly, and this data can slash the time spent recalling faulty products.
And never stop testing. Random samples, stress tests, and spot checks uncover design flaws that data alone can’t. When something slips through, record it—don’t hide it. Lessons learned from product failures turn into competitive advantages later. Only 49% of companies, according to a 2023 McKinsey poll, systematically use “failure analysis” to improve new designs. That’s a lot of opportunity left on the table.
Plant & Planning: The Space and Strategy That Bring It Together
This is where the action happens: your physical plant, and the magic of planning. Location, layout, and even little details like floor material impact cost and flow. Have you ever seen a shop where people waste steps hauling goods back and forth? That’s wasted energy and time. Smart plants arrange equipment so material moves in one direction, minimizing traffic jams and confusion. A 2024 MIT study found optimized layouts in midsize manufacturers led to a 17% drop in internal transport time.
But the plant is useless without planning. This is the choreography of the 5 Ps—a system that aligns materials, labor, machines, and deadlines. Without proper planning, even the most high-tech facility turns into a stress zone. Demand forecasting, material purchasing, maintenance schedules, shift patterns—it’s a juggling act. Modern Manufacturing ERP systems track thousands of moving parts in real time. According to Gartner, companies using advanced planning software saw a 22% reduction in late orders over 2023-2024.
Planning isn’t just about spreadsheets or software. It’s about what-if scenarios: What if a supplier goes bust? What if power goes out? Good plans have built-in backups—secondary suppliers, ready-made repair kits for critical machines, or flexible labor options. “Capacity flexibility” saved several European manufacturers in 2020, when COVID-19 disrupted parts supply. Those with nimble planning switched suppliers or ramped up alternate lines instead of grinding to a halt.
To get practical, plant managers run monthly “what went wrong” meetings. They use simple tables to track root causes and recurring snags. One company, for example, tracks these issues like this:
Issue | Root Cause | Resolution |
---|---|---|
Machine downtime | Lack of preventive maintenance | Scheduled weekly checks |
Late raw materials | Single supplier | Added secondary suppliers |
Order picking errors | Poor labeling | Color-coded bins |
Plant and planning decisions are rarely perfect, but tracking, naming, and fixing issues steadily lifts performance across months and years. The key? Review and adapt. No plan is set in stone, and sticking to a bad plan is usually worse than no plan at all.

Performance: Measuring What Matters—And Acting on It
It’s tempting to focus on busy-ness rather than true performance. But unless you measure what matters, you’re steering blind. Here’s where the fifth P earns its weight. Performance in manufacturing isn’t about how hard your machines work, it’s about what actually reaches your customer—quality, reliability, and cost all count.
The best use Key Performance Indicators (KPIs) to track progress. Some heavy hitters:
- On-Time Delivery Rate
- First Pass Yield
- Overall Equipment Effectiveness (OEE)
- Scrap and Rework Percentages
- Inventory Turnover
OEE is a favorite because it rolls up availability, performance, and quality into one percentage. High OEE means your process is humming, and you’re not bleeding money on hidden inefficiencies. World-class OEE looks like 85% or above. In 2024, most factories run closer to 60-70%, which means a lot of room for improvement.
Don’t drown in data, though. Pick metrics tied to your real pain points. Is late delivery killing your reputation? Focus on order cycle time. Quality slips after midnight shifts? Break down data by shift or crew. Show your team the numbers. When performance is out in the open, pride will drive better results than any speech. Audi’s Mexico plant famously displays live OEE boards across the factory—shifts compete to do better, and downtime drops as a result.
Here’s a tip: Celebrate wins. If your rework drops 10% in a month, throw a pizza party. Personal recognition, even a shoutout or a coffee card, goes a long way. It’s not about bribing people—everyone likes to see their hard work noticed. At the same time, dig into the root causes of poor performance. Firing off warnings won’t fix broken systems. Instead, gather the team, review what went wrong, and brainstorm solutions. Think of each dip in performance as a built-in feedback loop. Ignoring it lets weak points fester. Tackling it closes the gap before it hurts your bottom line.
So, those 5 Ps—5 Ps of manufacturing—they’re not just management buzzwords. They’re the building blocks of every thriving factory. People keep things running smooth, the process sets the rhythm, the product keeps your promise, the plant (and planning) is your home base, and performance is the scoreboard that steers improvement. Ignore any one, and cracks show fast. When all five click, you’re not just making things—you’re building a reputation, a customer base, and a business that lasts. That’s the power of the 5 Ps in action.