In today's fast-paced manufacturing industry, navigating through complexities requires a firm grasp on the fundamental 3 P's: People, Process, and Product. The synergy of these elements is central to achieving success in a sector that's continuously being reshaped by technological advancements and government initiatives.
With governments worldwide increasingly providing tools and frameworks to bolster these P's, it's more important than ever for businesses to understand how these schemes can be leveraged. This article sheds light on the intricate dance between these components and the policies designed to enhance them, offering insights that are both practical and forward-thinking.
- Understanding the 3 P's
- People: The Core of Manufacturing
- Process: Streamlining Efficiency
- Product: Driving Innovation
- How Government Schemes Integrate the 3 P's
- Real-world Applications and Strategies
Understanding the 3 P's
The concept of the 3 P's in manufacturing is a time-tested framework that stands as a cornerstone in the industry. At its core, these elements—People, Process, and Product—interact to create a dynamic ecosystem where productivity and innovation thrive. Each element is interdependent, supporting the others to drive forward momentum. But what do these P's truly represent, and why are they so crucial in the realm of modern manufacturing?
People are the life force behind every manufacturing operation. Without skilled individuals, even the most advanced technology remains idle. The emphasis here is on investing in human capital, offering training and development to equip the workforce with cutting-edge skills. For instance, the implementation of AI and automation calls for a new breed of technicians who are not only adept with machines but also understand complex data analytics. According to a recent study by MIT, companies that prioritized upskilling their employees reported productivity gains of up to 20%. This highlights how essential it is for any high-functioning manufacturing unit to invest in its people, ensuring they are both capable and motivated.
When it comes to processes, efficiency and adaptability are key. Manufacturing processes need to be streamlined to eliminate waste and maximize output. Lean manufacturing techniques, which focus on minimizing resource use while maintaining quality, have become commonplace. These methods require a deep understanding of the workflow from raw material to the finished product. Moreover, government schemes have been instrumental in advocating for clean and sustainable processes, offering incentives for adopting eco-friendly practices. It is interesting to note that companies that have embraced these green processes often see not just environmental benefits, but also increased profitability, with the World Economic Forum citing an average reduction of 16% in operational costs for such firms.
The product itself is the objective of combining both skilled people and efficient processes. Innovation in product design and functionality can set a company apart in a competitive market. The advent of smart manufacturing has led to products that are not only efficient but also intelligent, capable of adapting to user needs in real time. This evolution is supported by various government policies aimed at fostering innovation, such as grants for research and development. A quote from Dr. Jane Simmons, an industry expert, sums it up well:
"Innovation isn't just about creating something new; it's about creating something that responds dynamically to ever-shifting consumer needs."This shift ensures that products are not only relevant today but continue to meet future demands as well.
Acknowledging and effectively implementing the 3 P’s can lead to significant advances in manufacturing. Many global studies indicate that organizations which integrate these principles into their core strategies see higher rates of growth and sustainability. This is the reason why government schemes often prioritize the advancement of these areas, as they form the substratum of a thriving industrial sector.
People: The Core of Manufacturing
At the heart of any successful manufacturing enterprise lies an unwavering focus on People. It's not just about workforce numbers but the cultivation of skills, fostering innovation, and nurturing a collaborative environment. In today's manufacturing landscape, human capital is increasingly recognized as the most valuable asset. The implementation of meticulous personnel strategies, coupled with effective government schemes, can unleash a workforce's potential, driving a company towards new heights of productivity.
It's essential to understand the dynamics of workforce development in the context of government schemes. Governments across the globe have launched vocational training and upskilling initiatives to align workforce skills with the rapidly evolving technology in manufacturing. Initiatives like the European Skills Agenda aim to provide a green and digital transition, benefitting both employees and employers. By investing in education and training, nations prepare their workforce for the demands of current and future manufacturing challenges.
In many ways, ensuring the well-being and motivation of workers enhances productivity. Companies that create safe and supportive environments often see a significant impact on both efficiency and morale. As Richard Branson famously said,
"Take care of your employees and they'll take care of your business. It's as simple as that."This sentiment is echoed in industry practices where employee-centric policies drive innovation.
Government interventions often play a crucial role. By offering tax incentives and subsidies, they encourage manufacturers to invest in their people. These investments can be in the form of health benefits, on-the-job training opportunities, and creating pathways for career advancement. For instance, in the United States, the Manufacturing Extension Partnership focuses on helping small and medium-sized manufacturers with guidance on workforce development.
Additionally, diversity is now seen as a vital component of a thriving manufacturing environment. Companies actively embracing diversity outperform their peers in terms of innovation and adaptability. Programs that endorse diversity and inclusion help bring in varied perspectives, which are essential for creativity and problem-solving. Studies have repeatedly shown that diverse teams are able to tackle challenges in innovative ways that homogeneous teams may miss.
In the digital era, it's not just about inclusion but also about bridging the generational gap. Many manufacturing industries face challenges presented by a multigenerational workforce. While seasoned employees bring experience and wisdom, younger workers bring fresh ideas and adaptability to new technologies. Effective communication and mentorship programs foster an environment where both strengths are maximized.
All these aspects of People in manufacturing coalesce through effective leadership. Leaders who understand the nuances of these elements and can strategically guide their teams through change are invaluable. Thus, assembling a leadership team equipped to navigate the complexities of modern manufacturing is crucial. Through their guidance, the spirit of innovation, progress, and sustainability can flourish, ensuring the core of manufacturing—its people—remains strong and vibrant.
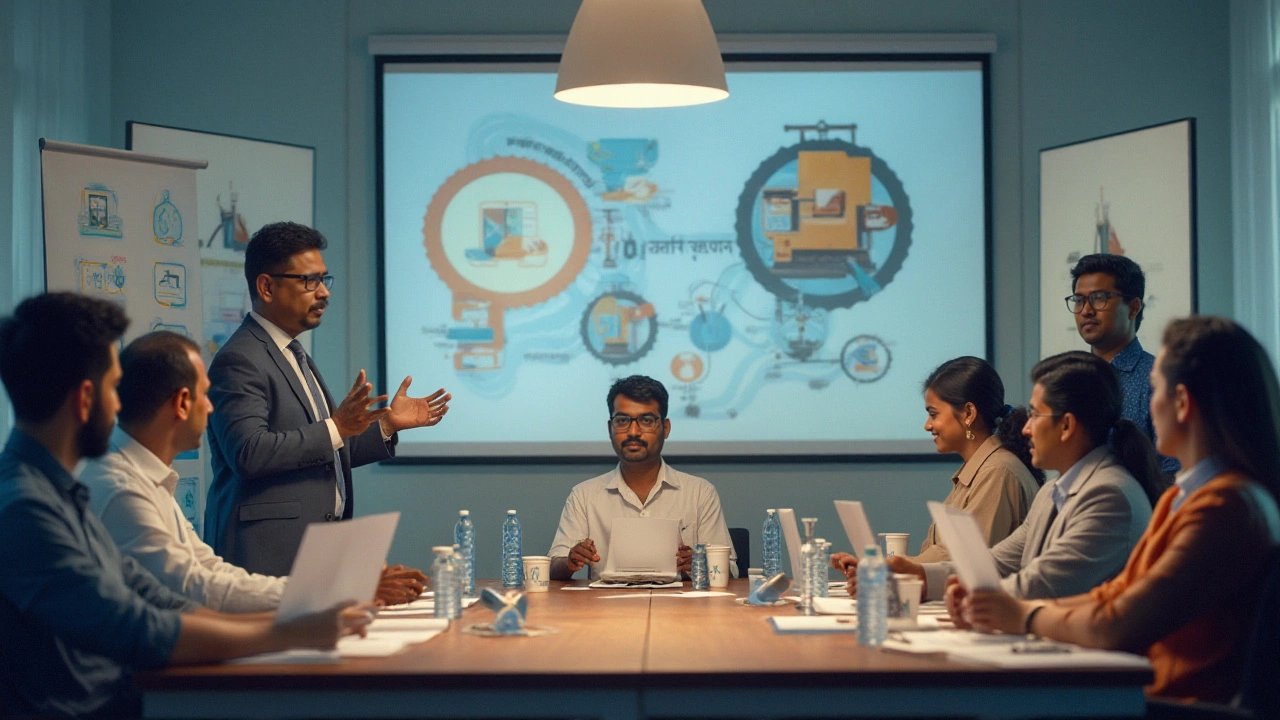
Process: Streamlining Efficiency
When it comes to manufacturing, the efficiency of the process is the heartbeat of productivity and success. The term 'process' covers a vast gamut of activities that range from the raw materials entering a facility to the final product leaving it. The ultimate goal is to ensure that every step along the way is as efficient and cost-effective as possible. Efficiency in processes not only reduces waste but also significantly cuts down production time, which is crucial in a competitive market where product demand can fluctuate rapidly. Companies that have perfected their processes often lean heavily on continuous improvement methodologies, such as Lean Manufacturing and Six Sigma, which emphasize reducing variabilities and defects to create smoother workflows and more reliable output.
One way businesses achieve streamlined manufacturing processes is through automation and the implementation of cutting-edge technologies. Automation eliminates manual errors, increases speed, and allows human workers to focus on more value-adding activities. Robotics and digital twins, which replicate physical processes in a digital space, are revolutionizing how manufacturers approach efficiency. According to a study by the International Federation of Robotics, the deployment of robots in manufacturing has increased productivity by an average of 20% over five years. Embracing technology not only boosts efficiency but also enhances a company’s ability to adapt to new challenges and shifts in the marketplace.
Government initiatives often play a crucial role in streamlining process efficiency. These schemes can range from financial incentives for adopting new technologies to providing training programs that focus on upskilling the workforce. The aim of these policies is to ensure that the workforce is not only adept at operating advanced machinery, but also proficient in identifying and executing process improvements. Take, for instance, the UK’s Manufacturing Made Smarter initiative, which offers grants and advice to manufacturers looking to innovate their processes. By aligning with such governmental support, companies can achieve remarkable strides in efficiency and stay ahead of the curve in industry competitiveness.
Another critical aspect of efficient processes is data analytics. By harnessing the power of big data, manufacturers can gain insights into every aspect of their operations. This data-driven approach allows them to pinpoint bottlenecks and areas for improvement with unprecedented accuracy. According to a report by McKinsey, manufacturers who effectively use data analytics see, on average, a 10% increase in production efficiency, which illustrates the profound impact smart data usage can have. This goes hand in hand with predictive maintenance strategies that use data analytics to foresee equipment failures before they occur, thus minimizing downtime and maximizing output.
It's important to recognize the human element in process efficiency as well. Training employees to think critically and offer solutions is just as crucial as implementing the latest technology. By fostering an environment where continuous improvement is a shared goal, companies can leverage their human capital to complement their technological advancements. Collaboration platforms help in sharing best practices across teams and departments, ensuring that every part of the organization moves in sync toward enhanced efficiency. This not only leads to better product quality but also to a more engaged and proactive workforce, which is key in maintaining long-term competitive advantage.
Product: Driving Innovation
When it comes to innovation in the realm of manufacturing, the product is the ultimate expression of creativity, practicality, and the market’s evolving needs. It's a testament to how effectively a company can blend cutting-edge technology with customer requirements. In the context of government schemes, innovative product development is encouraged and often subsidized. This initiative aims to not only stimulate the economy but also to ensure that industries stay competitive on a global stage. Many countries have launched special programs that back enterprises willing to push the boundaries in product design and function. For instance, the U.S. government's initiative focuses on high-tech manufacturing, explicitly funding projects that show promise in terms of invention and applicability.
At the heart of product innovation is user-centered design. Manufacturers are urged to dig deep into market research, diving into consumer behavior and preferences. This understanding helps in creating products that are not only technologically superior but also finely tuned to cater to specific demands. By closely analyzing these trends, companies can avoid the pitfalls of designing products that don't meet user expectations. Additionally, environmental considerations have grown to prominence, and incorporating sustainable practices in product development is now a key innovation driver. Products that align with green policies not only capture a socially conscious market but also qualify for certain governmental incentives.
"Innovation distinguishes between a leader and a follower," said Steve Jobs, underscoring the essential nature of product innovation in maintaining industry leadership. The relentless pursuit of better, more efficient, and smarter products has always been the backbone of industrial success.
In terms of practical implementation, manufacturers are exploring the realm of smart manufacturing. Technologies such as artificial intelligence and the Internet of Things (IoT) are transforming products into smart, connected devices. This trend is particularly notable in industries like automotive and electronics, where the integration of smart technologies has led to products like autonomous vehicles and smart home systems. For example, the rise of 3D printing technology has drastically changed how prototypes are developed, reducing both time and cost in the product development phase.
Another significant aspect of product innovation is collaboration. Many government schemes emphasize the importance of partnerships between academia, research institutions, and the private sector. Such collaborations are pivotal in driving advances that a single entity might find challenging to achieve on its own. Programs in countries like Germany have excelled in fostering such collaborative environments, often resulting in breakthroughs in sectors like biotechnology and clean energy.
Finally, continuous feedback loops are critical in this era of rapid innovation. The product development cycle is not linear anymore; instead, it becomes an iterative process. Feedback from initial prototypes is used to tweak and refine products ensuring they are market-ready and meet consumer expectations. This approach is critical in maintaining competitive advantage in a time when technological obsolescence is as quick as innovation itself. Companies embracing this agile approach often set the trend rather than follow it, solidifying their standing in the market.
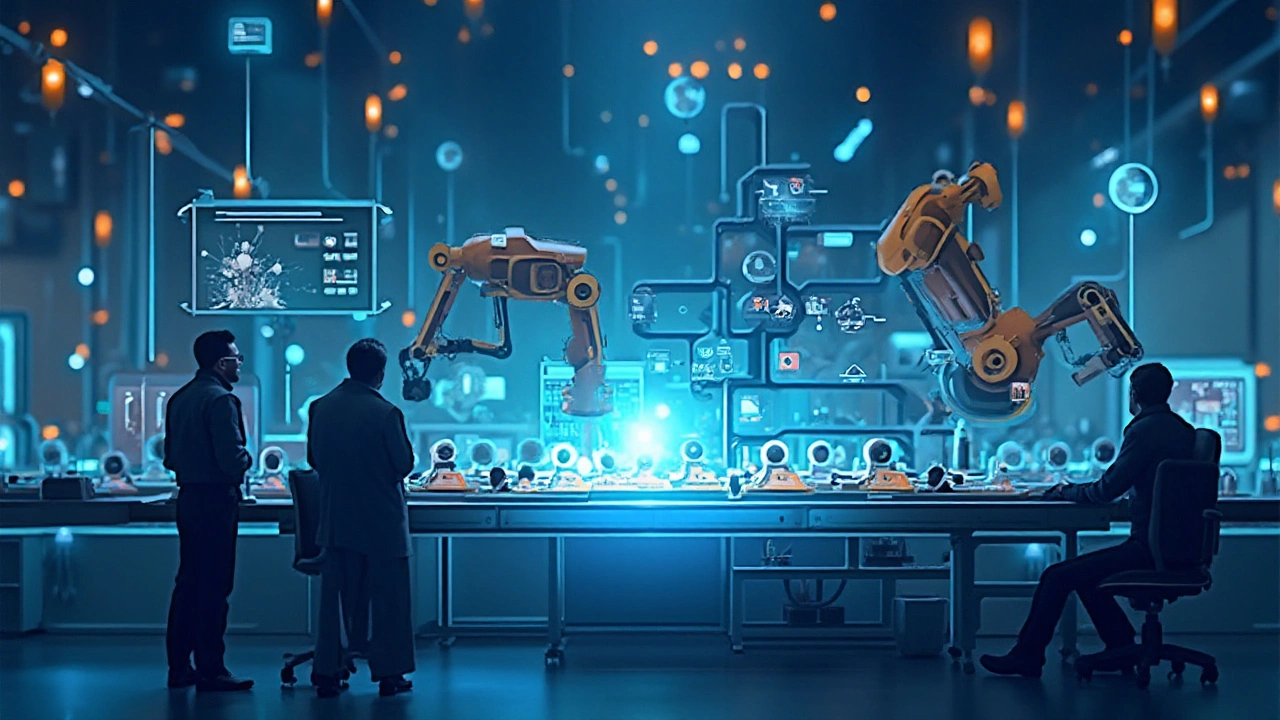
How Government Schemes Integrate the 3 P's
The intricate world of manufacturing is bolstered significantly by various government schemes that integrate the 3 P's: People, Process, and Product. These programs aim to promote growth and efficiency across the manufacturing sector, which is a cornerstone of many national economies. One of the key strategies involves investment in workforce development, as training and upskilling initiatives are essential to empower people and keep pace with technological changes. Governments often provide subsidies and tax incentives to encourage businesses to invest in their employees. By doing so, they cultivate a highly skilled workforce that is capable of driving innovative processes forward.
On the procedural front, modern governments deploy schemes that focus on streamlining operations and encouraging sustainable practices. Such initiatives typically include grants for adopting advanced technologies like automation and AI, which can dramatically enhance operational efficiency. Moreover, environmental regulations are designed to encourage businesses to implement eco-friendly practices, which not only benefit the planet but also often lead to cost savings in the long term. This dual approach ensures that manufacturing processes remain both competitive and responsible.
When it comes to the product aspect, innovation is at the heart of many government-backed initiatives. Support can come in the form of research and development credits or direct funding for projects that aim to bring cutting-edge products to market. These schemes are typically designed to reduce the financial barrier to innovation and help companies take bold steps that they might otherwise shy away from. By fostering a climate of experimentation and progress, governments help ensure that local industries remain competitive on a global scale.
Real-World Examples
One noteworthy example of integrated government support is the Manufacturing USA initiative in the United States, which connects industry, academia, and government to co-develop cutting-edge manufacturing technologies. This type of collaboration exemplifies how procedural and product-centric strategies can intersect to yield tangible improvements in manufacturing capabilities. In Europe, the Horizon 2020 program has been pivotal, offering billions in research funding to promote innovation across various fields, including manufacturing. These examples highlight the diverse methods through which government schemes can provide crucial support to enhance efficiency and technological advancement.
With these multi-faceted approaches, it's clear that understanding how government schemes are structured can provide businesses with the knowledge they need to capitalize on available opportunities. Such an alignment ensures that initiatives are not only beneficial for companies but also for the broader economy and society at large. A thriving manufacturing sector, built on the strong foundation of the 3 P's, thus becomes both a national and international asset.
Real-world Applications and Strategies
In the realm of manufacturing, translating the conceptual 3 P's into tangible outcomes isn't just theoretical; it's the backbone of how industries can stretch their capabilities. Let's take a look at some of the fascinating strategies that have been successfully implemented globally. A notable shift has been towards automation, which skillfully marries process improvements with enhanced product quality. Companies like Tesla have capitalized on automation to streamline their electric vehicle production lines. This fusion not only cuts down manufacturing times significantly but also increases the precise repeatability of intricate tasks that human hands might find challenging.
Another powerful strategy lies in the adoption of lean manufacturing principles. Toyota's production system, for instance, has been a paragon of efficiency, emphasizing waste reduction which aligns seamlessly with process optimization. By implementing kanban—a scheduling system for lean production—Toyota has not only kept inventories under control but also ensured a balanced flow in production, leading to greater productivity. What makes these practices noteworthy is their adaptability across various sectors from automotive to tech gadgets. It's about leveraging the strengths of the 3 P's to bring about a cohesive and improved structure.
Government-backed initiatives have also played a revolutionary role in this transformation, particularly in providing financial incentives and resources for sustainable practices. Take Germany's 'Industrie 4.0' as a sterling example. It encapsulates the digital transformation of manufacturing, creating smart factories with cyber-physical systems and Internet of Things technologies. This initiative not only bolsters the manufacturing prowess of companies but also integrates smaller businesses into this ecosystem to drive collective growth. According to a report by McKinsey, companies adopting these digital strategies could see a potential reduction of up to 15% in maintenance costs, a testament to the effectiveness of integrating technology into traditional systems.”
"Digital transformation is more than just a trend; it’s a mandate for survival," says Klaus Schwab, Founder of the World Economic Forum. "Those who succeed in developing a comprehensive digital strategy will maintain a competitive edge in the market."
Looking at another real-world success story, consider Unilever's approach to packaging and product sustainability. By aligning its operations with global sustainability standards and embracing circular economy practices, Unilever steadily enhances its product lines while reducing environmental impact. For other industries seeking to follow suit, the message is clear: the drive towards sustainability is not just environmentally friendly but economically prudent. Embracing the 3 P’s with a focus on eco-friendliness meets consumer demand while supporting business longevity.
Finally, a strategic move many companies are making involves collaborations and partnerships. By creating synergies with other organizations, businesses can share their expertise and resources to foster innovation. For instance, partnerships between manufacturing companies and technology firms often lead to the creation of state-of-the-art facilities that push the boundary of what's possible in production. This strategy not only enhances process efficiencies but also catapults the creation of cutting-edge products that serve a broader market base. These partnerships have become crucial especially in addressing technical challenges and accessing new markets.