As we stand midway through the 2020s, the call to breathe new life into American manufacturing echoes louder than ever. Once touted as the backbone of the nation's economy, manufacturing in the U.S. has seen its share of ups and downs over the decades. The vibrant hum of assembly lines across the country tells tales of bygone eras where local industries thrived, offering stable jobs and contributing significantly to local economies.
But, times have changed. Globalization, technological advancements, and shifting economic priorities have transformed the landscape. Yet, a renewed sense of optimism pervades the air. Policymakers, industry leaders, and workers alike are questioning: can America regain its manufacturing prowess?
In this exploration, we'll delve into the historical trajectory that shaped today's industry, discern how current government initiatives might spur a renaissance, and consider the innovation hurdles that lie ahead. Through these lens, we aim to provide a clearer picture of what lies ahead for American manufacturing, not only in terms of challenges but also the untapped potential waiting to be harnessed.
- Historical Context of U.S. Manufacturing
- Government Efforts and Policies
- Technological Innovations and Challenges
- Global Competitive Landscape
- Workforce Training and Development
- Looking to the Future: Opportunities and Threats
Historical Context of U.S. Manufacturing
The roots of American manufacturing run deep, intertwined with the nation’s development from its earliest days. In the late 18th century, the industrial spirit began with the introduction of mechanized textile production, paving the way for innovation. This momentum rapidly expanded through the 19th century, as industries like steel, construction equipment, and automobile manufacturing became cornerstones of the U.S. economy. Towns sprouted and thrived around factories, creating bustling hubs of activity and growth. It wasn’t just about production; it was about invention and transforming raw materials into goods that connected communities and defined livelihoods.
By the mid-20th century, the United States had established itself as the world's manufacturing powerhouse. This era, often dubbed the golden age of American manufacturing, was marked by significant economic expansion and innovation. The auto industry, led by giants like Ford and General Motors, transformed not only transportation but also the nation’s identity. Skilled labor was abundant, and the promise of a stable, well-paying factory job was a driving force behind the flourishing middle class. Yet, the winds of change were on the horizon, as the latter part of the 20th century presented new challenges.
As globalization took hold in the 1980s and 1990s, the manufacturing sector began to experience a marked shift. Companies sought cost efficiencies, leading to the offshoring of production to countries with cheaper labor costs. This trend reshaped the landscape significantly, resulting in a decline in manufacturing jobs within the U.S. The transition wasn't merely economic; it had profound social impacts, affecting communities built around these industrial jobs, and often leaving an enduring sense of loss. "The wave of offshoring in the late 20th century was a strategic economic move that prioritized short-term gains over long-term industrial sustainability," noted Harvard economist Dani Rodrik.
Despite these changes, American manufacturing did not come to a halt. Instead, it evolved, focusing on high-tech industries, advanced manufacturing processes, and innovation-driven sectors. Companies began to implement automation and digitization, adapting to a competitive global market. Recent years have seen a renewed interest in reassessing the role of domestic manufacturing, prompted by economic nationalism and the recognition of potential vulnerabilities in a globally stretched supply chain. This historical dance of growth, adaptation, and resilience frames today’s discussions about reigniting America's industrial flame and offers perspective as current strategies are crafted for a hopeful revival.
Government Efforts and Policies
In recent years, the United States government has made significant strides in addressing the slump in the American manufacturing sector, recognizing its crucial role in economic growth and job creation. One major initiative is the multifaceted 'Manufacturing USA' program, which sets the stage for revamping the industry through public-private partnerships. This network of manufacturing innovation institutes works tirelessly on promoting advanced manufacturing while fostering an ecosystem conducive to innovation, training, and competitive growth.
Another pillar supporting the manufacturing renaissance comes in the form of tax reform and incentives. Various policies have unfolded to assure companies that returning production to domestic soil can be profitable. Under the Tax Cuts and Jobs Act, corporate tax rates were lowered and new opportunities were introduced for businesses investing in American-made products and technologies. These policy shifts have piqued the interest of numerous industries, from textiles to electronics, hoping to revamp production processes with a national flair.
The 'Make it in America' plan provides an exemplary case of government encouragement in the transition back to homegrown manufacturing. Through deliberate cross-agency collaboration involving the Department of Commerce and the Small Business Administration, funds and resources are funneled toward regions with potential for industrial growth. Noteworthy is their focus on training programs, ensuring that workers possess the skills needed to thrive in a modern manufacturing environment.
Prominent advocates of such policies argue that a strong manufacturing sector reduces dependency on overseas production while bolstering national security. These strategic moves not only stimulate economic progress but also pave the way for technological advancements that enhance production efficiency and environmental sustainability. Secretary of Commerce Gina Raimondo remarked,
"In these plans lies the pathway to bringing families closer to secure, well-paying jobs, while safeguarding our independence in an increasingly interconnected world."Her words echo the sentiment driving the various policies targeting a manufacturing revival on American soil.
A significant challenge in this endeavor remains balancing short-term gains with long-term viability. While efforts to restore traditional manufacturing processes are essential, greater emphasis is placed on embracing technological integration to ensure sustainability in a competitive global landscape. To this end, the emphasis on workforce development through reskilling initiatives and apprenticeships is crucial. To truly capitalize on these government-backed policies, a concerted effort is required from industries and local communities in transforming rhetoric into productive results.
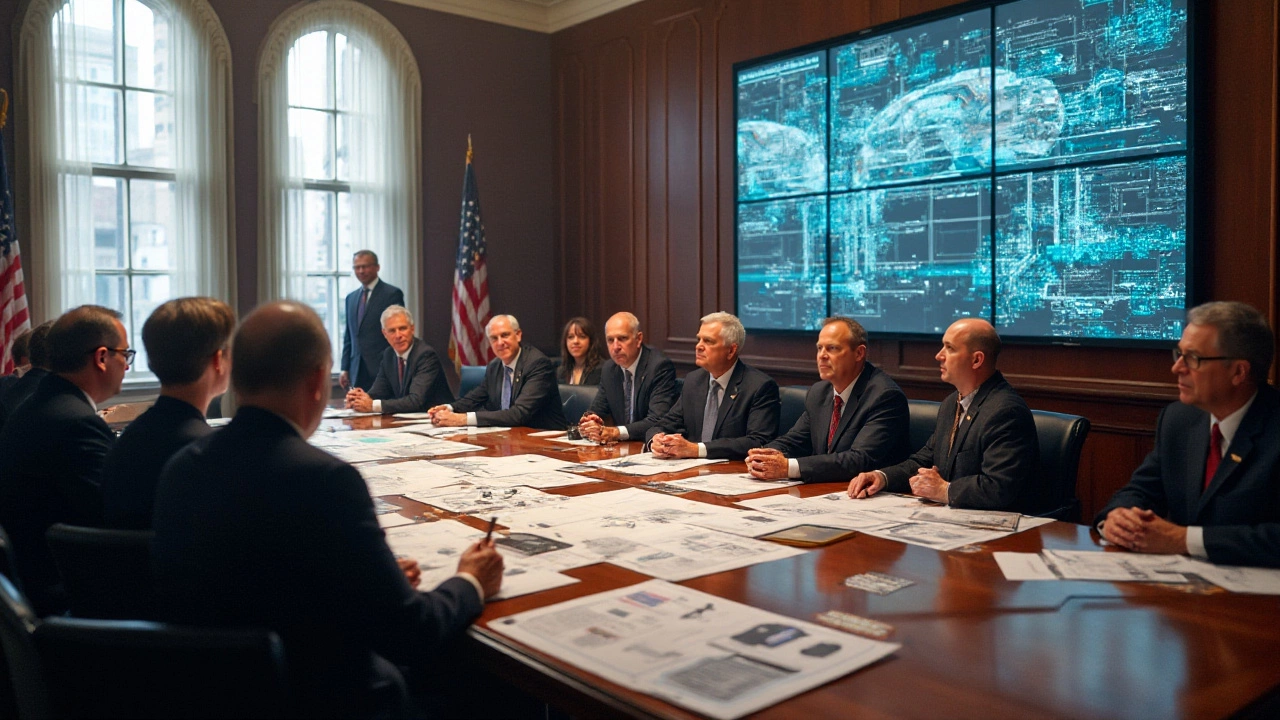
Technological Innovations and Challenges
In the realm of American manufacturing, technological innovations stand as both a beacon of opportunity and a formidable challenge. The automation revolution, driven by advancements in robotics and artificial intelligence, is reshaping production processes across the board. Advanced robotics, for instance, have made it feasible for factories to operate with unparalleled precision and efficiency, reducing error margins significantly. Yet, these machines require substantial investments—financial and educational—restricting smaller manufacturers from joining the technological bandwagon. As a consequence, the digital divide becomes more pronounced, leaving behind those who struggle to keep pace with rapid advancements.
Moreover, the advent of the Industrial Internet of Things (IIoT) has introduced a new era of interconnected devices, presenting an avenue for unprecedented data collection and analysis. This data-centric approach empowers manufacturers to optimize operations, predict future failures, and maintain predictive maintenance schedules. However, this sea of change comes with its hurdles. Cybersecurity threats loom large, as increased connectivity often translates into heightened vulnerability. As industry leaders like Tony Blevins noted, "The potential of IIoT is immense, but so is the complexity and the risk it introduces." Such realities underscore the perpetual balancing act between leveraging technology for growth and safeguarding against its inherent risks.
The rise of technologies like 3D printing also heralds a transformative potential. Additive manufacturing, as it is officially known, allows for customized production at unprecedented speeds, reimagining how products are conceptualized and realized. Industries ranging from aerospace to healthcare have begun to harness this, fostering innovation pipelines previously stymied by traditional manufacturing constraints. The challenge, however, lies in scaling these technologies to mass production levels. Current setups often favor bespoke manufacturing over traditional high-volume production, highlighting the need for continued research and development toward scaling up.
Parallel to these innovations is the constant evolution of sustainable manufacturing practices. The pressure to reduce carbon footprints and embrace eco-friendly methods is more intense than ever. Incorporating renewable energy and waste reduction technologies is now at the forefront of industry objectives. Yet, achieving this green transition requires overcoming challenges related to cost and implementation. Notably, transitioning to sustainable materials might incur higher costs, yet more brands are acknowledging that it is a necessary investment for long-term viability. Furthermore, data from recent industry reports underline that companies adopting eco-friendly practices have witnessed a 15% boost in consumer trust, reflecting the societal demand for sustainability.
Ultimately, for American manufacturing to not only adapt but thrive in this rapidly shifting technological landscape, there must be concerted efforts aligned with both innovation and education. Equipping the workforce with skills to handle new technologies is paramount. Partnerships between educational institutions and industry can bridge this gap significantly. Manufacturing workshops and programs centered around the latest technologies are crucial, ensuring workers are not only exposed to advancements but are also adept at integrating them into daily operations. Only by intertwining technology with human expertise can manufacturing in America anticipate surmounting these current challenges.
Global Competitive Landscape
The global manufacturing stage is akin to a complex, ever-evolving chessboard where nations play strategic moves to carve their economic dominance. American manufacturing, once the king of this board, is challenged today by emerging and established players alike. For decades, the tide of globalization swept across industries, favoring countries with abundant labor at lower costs. China, affectionately termed the 'world's factory,' witnessed a meteoric rise in its manufacturing sector, primarily due to its ability to produce goods cheaply and in massive quantities. As of 2023, China remained the leading manufacturing hub, but the winds of change are sweeping across this landscape.
Interestingly, the allure of low-cost production has gradually diminished in some regions. Countries like Vietnam and Bangladesh, with lower wage structures, are emerging as significant contenders, siphoning off manufacturing from places where rising labor costs have become a concern. Meanwhile, concerns about sustainability and ethical manufacturing practices are reshuffling priorities globally. These shifts are providing a window of opportunity for the United States to realign its industrial revival strategies, leveraging its strengths in advanced technologies and skilled labor force.
Despite these opportunities, challenges remain formidable. Tariffs and trade policies can bolster or hinder progress, and global supply chains suffused with intricate dependencies present both opportunities and vulnerabilities. The recent semiconductor shortages illustrated the fragility of global supply chains, exacerbating the need for strategic onshoring of critical manufacturing. According to the United Nations Industrial Development Organization, manufacturing activities contributed to approximately 16% of the global GDP in 2022, underlining its immense value in the world economy. To secure a competitive edge, American manufacturers are exploring high-tech, niche sectors, doubling down on automation, AI, and green technologies.
According to a report by the World Economic Forum, "Innovation in sectors like AI and advanced robotics will be key for nations wishing to excel in the next industrial revolution." These technologies enable precision manufacturing, reduce wastage, and provide high-quality products quickly—all critical factors for maintaining competitiveness globally.
The global arena necessitates agility and adaptability. As some nations clamor for protective trade practices, there is also a burgeoning trend towards regional partnerships and collaborations. The North American free trade zone stands as a testament to the benefits of regional integration, offering a counter-narrative to the volatilities of purely global supply chains. As the global competitive landscape continues to transform, the United States must strategically navigate geopolitical currents, striving to strengthen partnerships and fortify its position in the global manufacturing hierarchy.
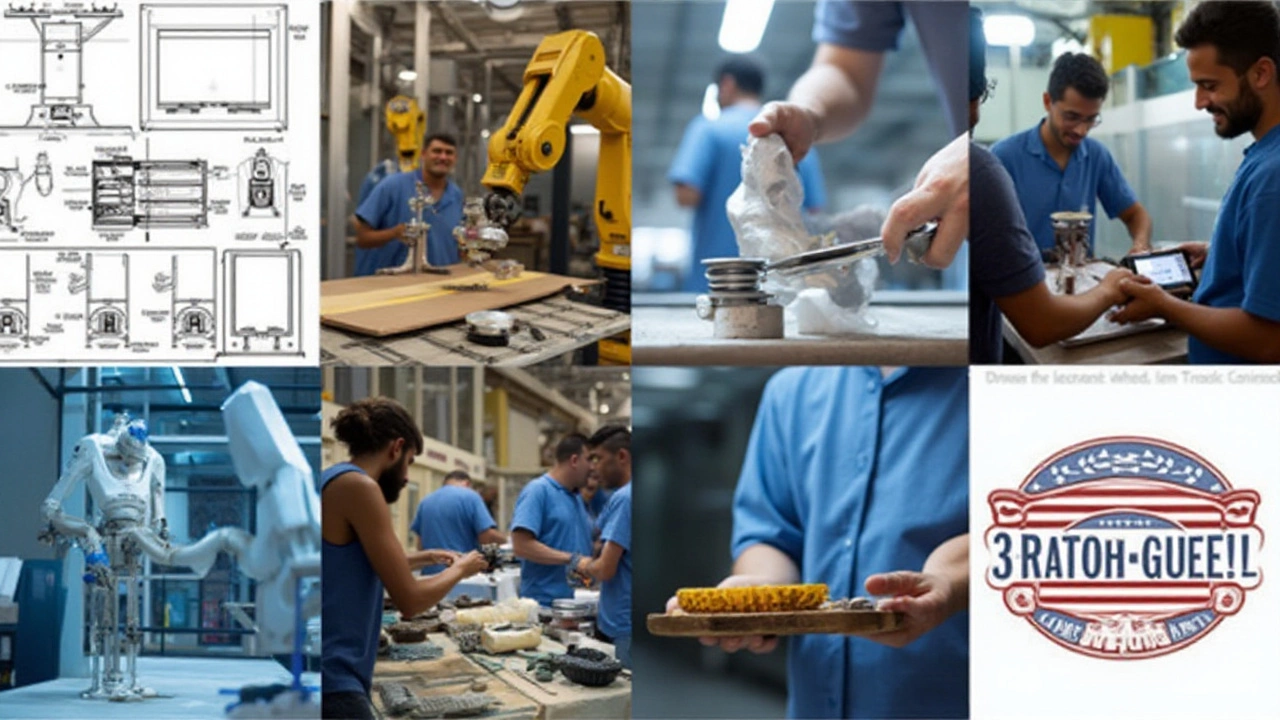
Workforce Training and Development
The revival of American manufacturing hinges not just on political and economic strategies, but significantly on the skills of the workforce manning the machinery. At its core, the quest to resuscitate manufacturing industries requires a strong focus on workforce training and development, adapting educational systems to meet the futuristic needs of manufacturing. Today's industries demand workers who are not just operators but technologists, adept at navigating the complexities of modern automated systems. Yet, a skills gap remains; a chasm that industries and educational institutions are striving to bridge.
To address this gap, numerous initiatives have emerged. Public and private sectors are increasingly partnering with educational institutions to design curricula that align with industry demands. High schools and community colleges are offering courses in robotics, advanced manufacturing technologies, and information technology, aiming to prepare students for the hybrid roles proliferating in today's manufacturing landscape. As America pushes for a renaissance, training programs like those implemented by the National Institute for Metalworking Skills (NIMS) have become essential, providing certifications that assure employers of a candidate's capabilities.
In a testimony before the Senate, the CEO of the Manufacturing Institute stated,
"Our future workforce is on a trajectory that integrates digital skills with traditional manufacturing expertise, creating a dynamic new class of manufacturing professionals."Such initiatives are complemented by government funding, which focuses on reskilling initiatives for older workers displaced by globalization and automation. This is crucial because transitioning from a labor-intensive environment to one driven by technology requires thoughtful and deliberate efforts to include workers from diverse backgrounds.
Apprenticeship programs, long a staple in Europe, have gained traction in the United States as well. Companies like Boeing and Siemens have forged strong programs in partnership with colleges, allowing students to earn while they learn, gaining invaluable hands-on experience even before stepping into their official roles. According to data from the United States Department of Labor, apprenticeship participants in the manufacturing sector have seen a steady increase, with more than 200,000 active apprenticeships recorded in 2023, a promising sign for industries aspiring for skilled talent.
Encouraging Lifelong Learning
Further, embracing a culture of lifelong learning and continuous improvement is paramount. As manufacturing technologies evolve at breakneck speed, staying current is a necessity. Many companies now incentivize learning, offering grants for courses and certifications that employees can pursue independently. They recognize that adaptable workers who thrive amid change are invaluable assets in sectors where agility is key.These steps are not in isolation. The seamless integration between skill development programs and local economies can have profound ripple effects. As more companies invest in tailored training, they can not only meet production demands but also bolster local job markets, increasing economic prospects for many communities.
Ultimately, fostering an environment of robust and adaptive learning is essential for the health of American manufacturing. As the nation strides towards a more innovative manufacturing future, equipping the workforce with right skills remains a vital task, demanding creativity, collaboration, and a clear vision for the future.
Looking to the Future: Opportunities and Threats
The future of American manufacturing holds a complex tapestry of both bright opportunities and shadowy threats. As the global landscape evolves, industries must adapt swiftly. A major opportunity lies in the growing consumer demand for locally-made products. This desire for "Made in America" is not just a trend; it represents a shift towards supporting local economies and ensuring product quality. Companies that can capitalize on this sentiment could carve out lucrative niches, encouraging more domestic production and job creation. Yet, this same opportunity presents challenges in scaling operations while maintaining cost efficiency, a delicate balance that firms must master.
Technological advancement is another beacon. The progression of smart manufacturing—driven by AI, IoT, and automation—offers the possibility to optimize production processes. This not only increases efficiency but also reduces waste. However, adopting these technologies requires substantial investment, posing a risk for smaller firms. There is also the question of how to upskill the current workforce to handle new technologies, which brings to light the pressing need for robust workforce training programs.
The geopolitical scene casts both a shadow and a light across the landscape. Trade relationships are increasingly turbulent, bringing unpredictability to global supply chains. Yet, this uncertainty can spur the U.S. to bolster its own production capabilities. A well-known business strategist, Michael Porter, once stated,
"The essence of strategy is choosing what not to do."This rings particularly true for manufacturers weighing whether to rely on global imports or to shore up domestic supply networks.
Government policies will play a decisive role. Initiatives providing incentives and support for industrial revival can pave the way for growth. Yet, legislative hurdles and budget constraints could stymie progress, making it crucial for entities to engage with policymakers to create a favorable environment. Social and environmental factors cannot be ignored either. Ethical manufacturing practices and sustainability are no longer optional. Companies that embrace green initiatives not only contribute positively to the planet but often find themselves rewarded with consumer loyalty and brand prestige.
Although much uncertainty exists, this uncertainty itself can drive innovation and resilience in manufacturing jobs. By nurturing a culture of adaptability and foresight, American manufacturing can position itself robustly in the tumultuous global stage. The next decade could indeed spearhead a new dawn for U.S. industries, where opportunities are seized, threats mitigated, and futures shaped by ingenuity and collaboration.