Imagine picking up almost any gadget or toy at home, flipping it over, and seeing 'Made in China,' Vietnam, or even Mexico. That’s not a coincidence. Outsourcing has long been a key part of how American companies keep prices down and products moving. But just how much of America’s manufacturing actually gets sent overseas? The answer is more tangled than you might think, weaving together stories of jobs, costs, politics, and plain-old habit.
What Exactly Is Outsourcing in U.S. Manufacturing?
Outsourcing gets thrown around a lot, especially during political debates. But let’s clear up what it means here. When we say a company outsources its manufacturing, it means parts or entire products are made outside the U.S., often by a third-party supplier, instead of in American factories. This isn’t the same as simply using a foreign supplier for one specific part; often, whole factories abroad are dedicated to producing items for American brands. Think Apple’s iPhones, which are mostly assembled in Chinese factories by Foxconn, or clothes from global brands made in Bangladesh or Vietnam. Even when you buy a car from an American brand, its parts come from all over—some seats from Mexico, electrical wiring from China.
This outsourcing trend isn’t new. In fact, it started ramping up in the 1970s and 80s, when companies realized it was way cheaper to make goods in places where wages and regulations were looser. By the late 1990s and early 2000s, outsourcing was in full swing, impacting everything from sneakers to electronics. According to the Bureau of Economic Analysis, every year, U.S. companies buy over $2 trillion in goods and services from overseas suppliers—much of that related to manufacturing.
A funny fact: Even though 'Made in USA' is a badge many people look for, according to the Federal Trade Commission, a product can carry that label if its final assembly is in the U.S., even if loads of its parts are made overseas. Basically, outsourcing isn’t just a total shift; it’s often a patchwork of parts made around the globe, stitched together back home or in a different country.
How Big is Outsourcing in American Manufacturing?
So, let’s get specific. According to data from the U.S. Bureau of Labor Statistics (BLS) and the Reshoring Initiative, somewhere between 25% and 30% of all U.S. manufacturing jobs were offshored in the past four decades. That’s millions of jobs—and billions in goods. Back in 2000, roughly 17 million Americans worked in manufacturing. Fast forward to 2024, and that number is hovering just above 12 million. While not all of those lost jobs went overseas (automation plays a role too), a solid chunk did.
In dollar terms, imports of manufactured goods into the U.S. topped $2.5 trillion in 2023, per U.S. Census Bureau data. Roughly 60% to 80% of the stuff American households buy—furniture, tech gadgets, clothes, toys—has some part built outside our borders. For electronics and apparel, the figure can edge even higher, past 90%, especially for items like smartphones and cheap fashion.
Here’s how some key categories look, based on the most recent stats:
Product Category | Estimated U.S. Market Outsourced (%) | Main Outsourcing Destinations |
---|---|---|
Electronics | up to 95% | China, Vietnam, Taiwan |
Apparel & Footwear | over 97% | China, Vietnam, Bangladesh, Indonesia |
Automobiles | ~40% (for parts) | Mexico, Canada, Germany, Japan |
Furniture | 85% | China, Vietnam, Mexico |
Toys | over 90% | China, Vietnam |
Pharmaceuticals | ~70% (for ingredients) | China, India |
Those numbers are wild, right? Take clothes for example. According to the American Apparel & Footwear Association, more than 97% of clothes sold in the U.S. are made offshore. Walk into any store—chances are, almost every tag will have a foreign country on it. Same with furniture and even essential goods like medicine, where as much as 70% of the active ingredients in U.S. drugs come from foreign labs.
Why so much outsourcing? For most companies, it’s all about cost. Labor can be up to ten times cheaper in China or Bangladesh than in Ohio or Texas. Mixing that with low-cost shipping (container ships are massive floating warehouses), it’s a no-brainer for companies trying to save a buck. But, as we saw during the pandemic, that comes with risks—like shipping delays or sudden shortages.
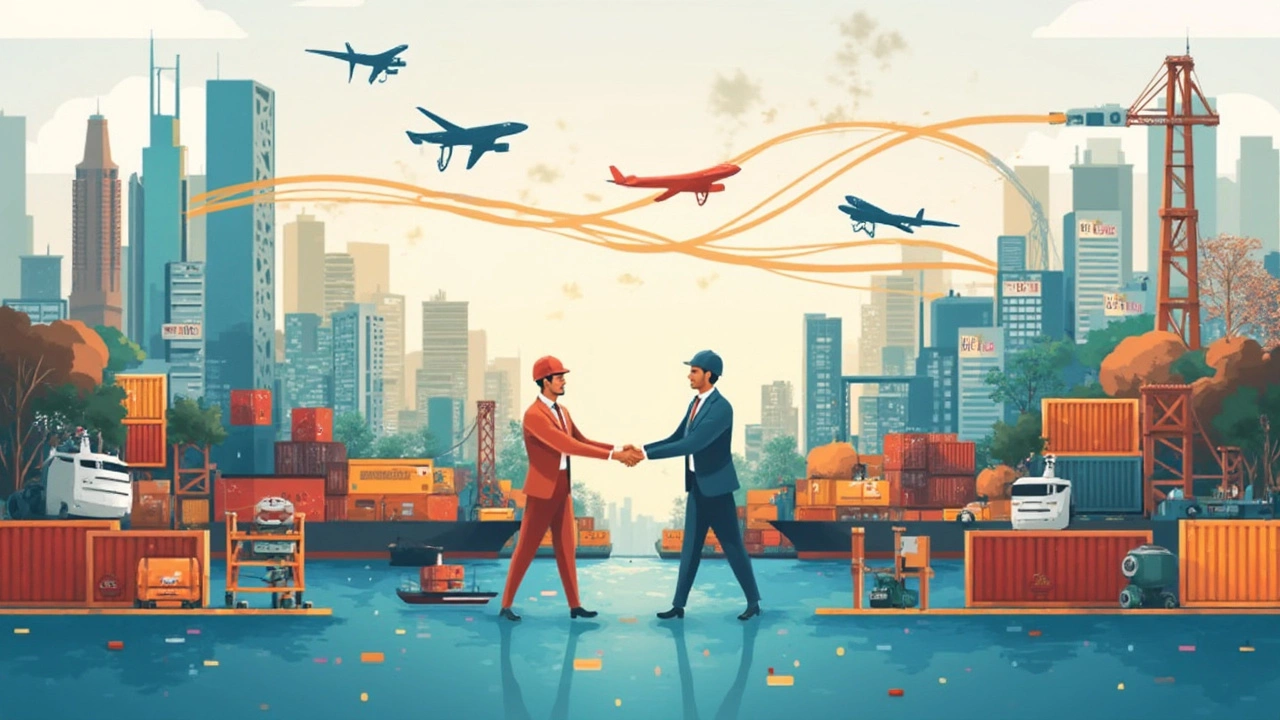
Why Companies Outsource – and the Impact on U.S. Jobs
We can’t ignore why outsourcing became a giant wave. For huge brands, every cent matters, especially in markets where buyers are used to affordable prices. Lowering production costs lets them invest more in tech, branding, or just push for bigger profits. Also, many countries now have specialized manufacturing hubs—think microchip 'cities' in Taiwan, or textile regions in Vietnam. These places get so good at what they do, even the best U.S. factories can’t always compete.
Of course, there’s a price. Workers feel it first. If you grew up near Detroit or in a Midwest factory town, you’ve probably seen entire neighborhoods hollowed out after plants closed or production moved to Mexico or Asia. Economists point out that outsourcing can boost productivity and lower prices, but for many families, the lost job isn’t easily replaced. Assembly-line factory gigs once supported entire communities, paying decent wages and benefits. Now, those same workers might have to settle for less stable, lower-paying work.
My son Rehan hears stories from his uncles about when everyone on the block worked at the same plant. Today, there’s no guarantee those jobs will come back. Outsourcing also changes the skills needed at home. Companies now look for folks who can manage logistics, do advanced robotics, or coordinate with international suppliers, rather than just run machines. The rise of robots has plenty to do with job losses too, but shipping work abroad is still a heavyweight factor.
Quick tip if you’re job-hunting or switching careers—look for roles connected with supply-chain management, robotics, or international trade. These jobs have popped up exactly because of how much business is done globally. The downside: They often require more education or technical skills than yesterday’s factory work.
What’s Changing: Nearshoring, Reshoring, and the Future of American Manufacturing
Now, here’s a twist. After decades of shipping jobs and production overseas, some U.S. companies are rethinking the whole outsourcing game. The last few years have been one long lesson in supply chain drama—pandemic lockdowns, shipping chaos, and sudden shortages woke everyone up to the real cost of being too reliant on foreign factories. Add in political pressure about 'bringing back American jobs,' tariffs that make imports pricier, and new tech that makes homegrown factories way more efficient.
This leads to two new trends you’ll probably hear about. The first is 'reshoring': moving some manufacturing back to the U.S. The second is 'nearshoring': shifting production closer, like to Mexico or even Canada, instead of far-off Asia. According to the Reshoring Initiative’s 2024 report, nearly 350,000 manufacturing jobs were announced as 'coming back' to the U.S. last year—the highest number on record. Companies cite everything from unstable overseas politics to high shipping costs, or that customers want to see more 'Made in USA' labels, especially on things like electronics, electric car batteries, or critical medicines.
Still, it’s way too early to call it a tidal wave. The share of actual production that’s moved back is still small—most companies go for a hybrid. Maybe one line of high-end products gets made at home, while bulk goods stay overseas. A cool example: Whirlpool builds premium washing machines in Ohio, but its basic models come from Mexico. Apple recently started making a small batch of iPhones in India, just to spread its bets beyond China.
Thinking about the future, new tech could play a big part. Automation, AI, and 3D printing make it easier to produce stuff in the U.S. without as many workers. But that still won’t solve the puzzle alone. Energy prices, government incentives, labor availability—all matter. Biden’s administration, for example, launched huge subsidies for U.S. chip factories to try and compete with Asia. Even so, most analysts think the global system is here to stay: companies will keep a blend of home and foreign suppliers, balancing costs with resilience.
If you want to shop as local as possible, check out the website of brands or look for real '100% Made in USA' programs. The cool part is, every dollar spent on U.S.-made stuff supports more local jobs than a cheap import does. But, expect to pay more for that pride. For now, the world’s supply chains are tangled on purpose—it’s cheaper, faster, and gives us more choices (but also more headaches when something goes wrong).
One thing’s clear: U.S. manufacturing rides a global rollercoaster. There’s money, politics, jobs, and even family stories tied up in where our stuff gets made. Next time you’re at the store, just flip over the box and ask yourself—who, and where, made this? The answer is pretty much always part American, part everywhere else.